Most organizations have inefficiencies in processes, and any improvement that can be adopted will help the business become more efficient and competitive.
Value stream mapping is a tool developed to help visualize and identify inefficiencies, enhance workflow, and improve overall productivity.
This article will provide value stream mapping’s definition as it is used today, how such a process can be applied, its benefits, potential issues and recommendations about its adoption, and relevant tools.
Jump to:
- What is Value Stream Mapping (VSM)?
- What are the Benefits of VSM or Value Stream Mapping?
- Value Stream Map: Practical Examples
- How to Create a VSM: The Value Stream Mapping Process in 7 Steps
- Key Tips For VSM
- What are the Challenges of Value Stream Mapping?
- Value Stream Mapping vs. Process Mapping
- Tools and Software For Value Stream Mapping
- Facilitate Value Stream Mapping With Ardoq
- FAQs About Value Stream Mapping
What is Value Stream Mapping (VSM)?
Value stream mapping (VSM) is a lean management tool that visually represents the flow of materials and information in a process from beginning to end. By mapping the current state of a process, it helps organizations identify waste, inefficiencies, and areas for improvement.
VSM originated from lean manufacturing principles, particularly within the Toyota Production System in the 1980s, when it was developed as a way to visualize and analyze the flow of materials and information in manufacturing processes. James Womack and Daniel Jones popularized the concept in their book “Lean Thinking”, emphasizing the importance of eliminating waste and enhancing value.
The value stream mapping definition and application has since evolved beyond manufacturing and VSM is now applied in various industries to improve processes, increase efficiency, and enhance customer value by systematically identifying and addressing inefficiencies.
What are the Benefits of VSM or Value Stream Mapping?
The use of VSM offers numerous benefits that enhance organizational efficiency and effectiveness. These include:
-
A clear visual representation of the entire process: This enables teams to identify value-added and non-value-added activities. This clarity helps in pinpoint waste, bottlenecks, and inefficiencies that can be addressed for improvement.
-
Fostering collaboration among team members: VSM encourages discussions about the process, leading to a shared understanding of workflows and challenges. This collaborative approach can enhance team dynamics and promote a culture of continuous improvement.
-
Identifying and prioritizing improvement initiatives: VSM highlights the most critical areas that impact overall performance. By focusing on these areas, organizations can achieve quicker results and a higher return on investment.
-
Reduced lead times, improved quality, and increased customer satisfaction: Processes become more streamlined and responsive to customer needs.
-
Foundation for further lean initiatives: VSM provides a structured approach to ongoing process optimization.
Overall, the benefits of VSM contribute to a more efficient, effective, and customer-focused organization.
Value Stream Map: Practical Examples
A value stream map can be utilized across different industries to optimize processes and enhance value delivery:
1. Manufacturing Process: In a manufacturing setting, VSM can map the production of a specific product, such as an automobile.The map would detail each step in the assembly line, from the arrival of raw materials to the final inspection and delivery.
By analyzing the map, the team can identify delays, excess inventory, and non-value-added activities, leading to strategies for reducing lead times and improving overall efficiency.
2. Healthcare Services: VSM can also be applied in healthcare to improve patient flow in a hospital.
For instance, mapping the patient admission process, treatment, and discharge can reveal inefficiencies such as long wait times or unnecessary paperwork.
By visualizing the entire patient journey, healthcare providers can streamline processes, enhance patient experience, and reduce costs while maintaining high-quality care.
Below is an example of how a typical order to cash value stream could be visualized:
How to Create a VSM: The Value Stream Mapping Process in 7 Steps
Value stream mapping steps typically involve the following:
-
Identify the Product or Service to map, ensuring the team understands its significance to the organization and customers.
-
Map the Current State by making a visual representation of the current process, detailing each step involved from start to finish. This includes identifying value-added and non-value-added activities and the flow of materials and information.
-
Analyze the Current State to identify waste, bottlenecks, and inefficiencies. Engage team members in discussions to gain insights into areas that require improvement.
-
Design the Future State map that outlines an optimized process. This should focus on eliminating waste, improving flow, and enhancing value delivery to the customer.
-
Create an Action Plan to implement the changes needed to achieve the future state. This includes assigning responsibilities, setting timelines, and determining necessary resources.
-
Implement Changes, making the necessary adjustments to processes and workflows.
-
Review and Adjust the new process continuously, gather feedback, and make adjustments as needed to ensure ongoing improvement and alignment with organizational goals.
Key Tips For VSM
For effective value stream mapping, the following actions are strongly recommended:
-
Involve the right people by engaging a cross-functional team that includes members from different departments involved in the process. Their diverse perspectives will provide valuable insights and foster collaboration.
-
Start with a straightforward process to map. This will help the team become familiar with VSM techniques before tackling more complex processes.
-
Focus on the customer to identify what adds value from the customer's perspective and prioritize improvements that enhance customer satisfaction.
-
Use standard symbols for processes, inventory, and information flow. This will help create a clear and easily understandable map.
-
Identify metrics such as lead times, cycle times, and inventory levels on the map. This data will help analyze the current state and measure improvements.
-
Highlight waste, such as delays, excess inventory, and unnecessary steps. This will make identifying opportunities for improvement less complicated.
-
Iterate and improve by treating VSM as an ongoing process. Regularly revisit and update the maps as processes change and improvements are implemented.
By following these suggestions, organizations can effectively utilize VSM to enhance their processes and drive continuous improvement.
What are the Challenges of Value Stream Mapping?
VSM can present several challenges to an organization.
-
Resistance to Change: Employees can be reluctant to accept changes in established processes, fearing disruptions or additional workload. Overcoming this resistance requires effective communication and team members' involvement in the mapping process.
-
Data Accuracy and Collation: Gathering accurate and comprehensive data for the current state map can be time-consuming and challenging. Incomplete or inaccurate data can lead to misleading conclusions and ineffective improvement strategies.
-
Complexity: Mapping complex processes with multiple steps and interactions can be overwhelming. Simplifying the process without losing critical details is essential for creating an effective map.
-
Maintenance: After implementing changes based on the VSM, maintaining those improvements can be difficult. Organizations must foster a culture of continuous improvement and regularly review processes to ensure ongoing efficiency.
-
Scope: Focusing too narrowly on a single process may overlook broader organizational issues. It's important to consider how the mapped process interacts with other organizational processes.
-
Lack of training and resources: Not all team members may be familiar with VSM techniques or Lean principles, so providing adequate training and resources is crucial for successful implementation.
Addressing these challenges can enhance the effectiveness of VSM and lead to meaningful process improvements.
Value Stream Mapping vs. Process Mapping
Process and value stream mapping are both tools used to visualize and analyze processes, but they serve different purposes and focus on different aspects. Key areas of difference include:
1. Focus
VSM emphasizes the flow of materials and information in a process, specifically identifying value-added and non-value-added activities. It aims to optimize the entire value stream to enhance customer value and eliminate waste.
Process Mapping details the specific steps and tasks involved in a process. It provides a step-by-step breakdown of how a process operates, often without directly emphasizinga direct emphasis on value or waste.
2. Purpose
The primary goal of VSM is to improve efficiency and effectiveness by visualizing the entire value stream and identifying areas for improvement that enhance customer satisfaction.
The goal of Process Mapping is to document and understand how a process works, which can help in training, standardization, and identifying potential areas for improvement.
3. Level of Detail
VSM typically provides a higher-level overview of the process, focusing on the flow of value rather than every individual task.
Process Mapping provides a more detailed view of each step in the process, including decision points, roles, and responsibilities.
Below is a visual example of how a value stream overlaps with but also differs from a process:
In summary, while VSM and Process Mapping are valuable tools for process improvement, VSM focuses on optimizing the value stream and eliminating waste. In contrast, Process Mapping is concerned with documenting and understanding the specific steps in a process.
Tools and Software For Value Stream Mapping
Several tools and software options are available for VSM, ranging from simpler drawing tools to specialized software designed for lean management. Some of the popular choices are:
-
Microsoft Visio is a versatile diagramming tool that allows users to create detailed VSM diagrams using standard symbols and templates. It is widely used for various types of process mapping.
-
Lucidchart is an online diagramming application that enables collaborative VSM creation. It offers templates and shapes specifically for value stream mapping, making it easy to visualize processes.
-
Miro is a collaborative online whiteboard platform that allows teams to create VSMs in real-time. It provides various templates and tools for brainstorming and mapping processes.
-
LeanKit is a Lean project management tool with features for creating value stream maps. It helps visualize workflows and manage Lean initiatives effectively.
-
iGrafx is a business process management application that includes VSM capabilities. It allows users to model, analyze, and optimize processes.
-
SmartDraw is a diagramming tool that offers templates for VSM and other process mapping techniques. Its easy-to-use interface allows users to create professional-looking maps.
-
VSM Software is specialized software specifically designed for VSM. It offers features tailored to Lean practitioners, such as real-time collaboration and value stream mapping analysis tools.
These tools can help organizations create and analyze value stream maps, facilitating process improvement initiatives.
Facilitate Value Stream Mapping With Ardoq
Ardoq can facilitate VSM through several built-in features and capabilities that visualize processes and manage information. Get a high-level introduction to how VSM works in Ardoq:
Key areas that Ardoq helps with VSM include:
-
Use the modeling features to create visual representations of value streams, mapping out the current state of processes, including all steps, inputs, outputs, and stakeholders involved.
-
Multiple users can collaborate in real-time, enabling cross-functional teams to contribute their insights and expertise and ensuring a broadcomprehensive view of the value stream.
-
Identify value and waste by highlighting value-added and non-value-added activities within the mapped processes. This helps identify areas of waste and opportunities for improvement.
-
Document metrics, such as KPIs within the platform’s data-driven dashboards, to enable efficient analysis of the current state and measure improvements over time.
-
Design future state of value streams, including proposed changes, optimizations, and elimination of wasteful activities.
-
Iterate and update the value stream maps as improvements are implemented to reflect changes and monitor progress. This supports a culture of continuous improvement.
By leveraging these features within Ardoq, organizations can effectively facilitate VSM, enhance collaboration, and drive process optimization initiatives.
Value stream mapping is a powerful tool for organizations aiming to improve efficiency and effectiveness. It allows teams to visualize processes, identify waste, and streamline workflows.
By highlighting bottlenecks and areas for improvement, it facilitates better decision-making, enhances collaboration, and ultimately leads to increased value delivery to customers.
Get in touch to learn more about how Ardoq can help you get better transparency over your organization’s value streams.
FAQs About Value Stream Mapping
What are the Key Components of a Value Stream Map?
Key components of a value stream map include the process steps in the workflow, the information flow, the material flow, lead times, and inventory levels.
How to Create a Value Stream Map
To create a Vvalue Sstream Mmap, the following important steps should be followed:
-
Select a Product or Service: Identify what is to be mapped.
-
Map the Current State: Identify and document each process step, including information and material flow.
-
Analyze the Map: Identify waste and inefficiencies.
-
Design the Future State: Outline improvements to optimize the process.
-
Create an Action Plan: Develop steps to implement changes.
-
Review and Update: Continuously monitor and adjust the map as needed.
What Is the Difference Between a Current-State and Future-State Value Stream Map?
The difference between a current state and future state value stream map lies in their focus and purpose. Current state VSM focuses on the existing process as it operates, whereas the future state illustrates the desired process after improvements are implemented.
The current state identifies inefficiencies, waste, and bottlenecks within the current workflow and serves as a baseline for understanding how the process functions and where improvements are needed. The future state outlines an optimized workflow that enhances efficiency, reduces waste, and increases value delivery to the customer. It serves as a goal for the organization to strive towards.
Finally, the current state includes all steps, information flows, material flows, lead times, and inventory levels as they exist today, while the future state outlines an optimized workflow that enhances efficiency, reduces waste, and increases value delivery to the customer. It serves as a goal for the organization to strive towards.
In summary, the current state map provides a snapshot of the present situation, while the future state map envisions an improved process.
Which Industries Benefit From Value Stream Mapping?
VSM is beneficial across various industries, including:
-
Manufacturing: It is used to help identify waste and optimize production processes, leading to increased efficiency and reduced costs.
-
Healthcare: It helps streamline patient flow, reduce wait times, and improve service delivery.
-
Software Development: Processes are enhanced by visualizing workflows, identifying bottlenecks, and improving collaboration.
-
Logistics: It helps optimize supply chain processes, improving inventory management and delivery times.
-
Retail: It enhances the customer experience by streamlining operations, reducing lead times, and improving inventory turnover.
How Often Should a Value Stream Map Be Updated?
A value stream map should be updated regularly to reflect changes in processes, workflows, and improvements. Typically, this would include periodic reviews after major changes, continuous improvement initiatives, and feedback loops.
Can VSM Be Used For Digital and Service-Based Processes?
VSM can effectively be used for both digital and service-based processes. While it originated in manufacturing, its principles are applicable across various industries.
Digital processes help visualize workflows in software development, IT services, and digital marketing, identifying inefficiencies in coding, testing, deployment, and customer feedback loops. Service-based processes can be mapped out, from customer inquiries to service delivery, to help identify bottlenecks, streamline operations, and enhance customer satisfaction.
How Long Does it Take to Complete a Value Stream Map?
The time it takes to complete a VSM can vary significantly based on several factors, including the complexity of the process being mapped, the size of the team involved, and the level of detail required. Generally, the process can take a few hours to several days.
Overall, the duration depends on the specific context and the thoroughness of the mapping effort. Regular updates and reviews will also require additional time in the future.
- PDF Guides Emerging Technology Adoption Report 2024 Navigating Turbulent Times With Digital Business Optimization
- Blog Posts Differences Between Business Capabilities, Processes, & Value Streams Ardoq Expands Business Process Transformation Capabilities With New Acquisition and Comprehensive Suite for Mapping and Modeling Solutions
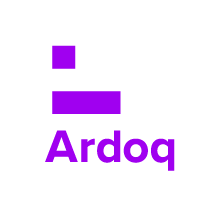